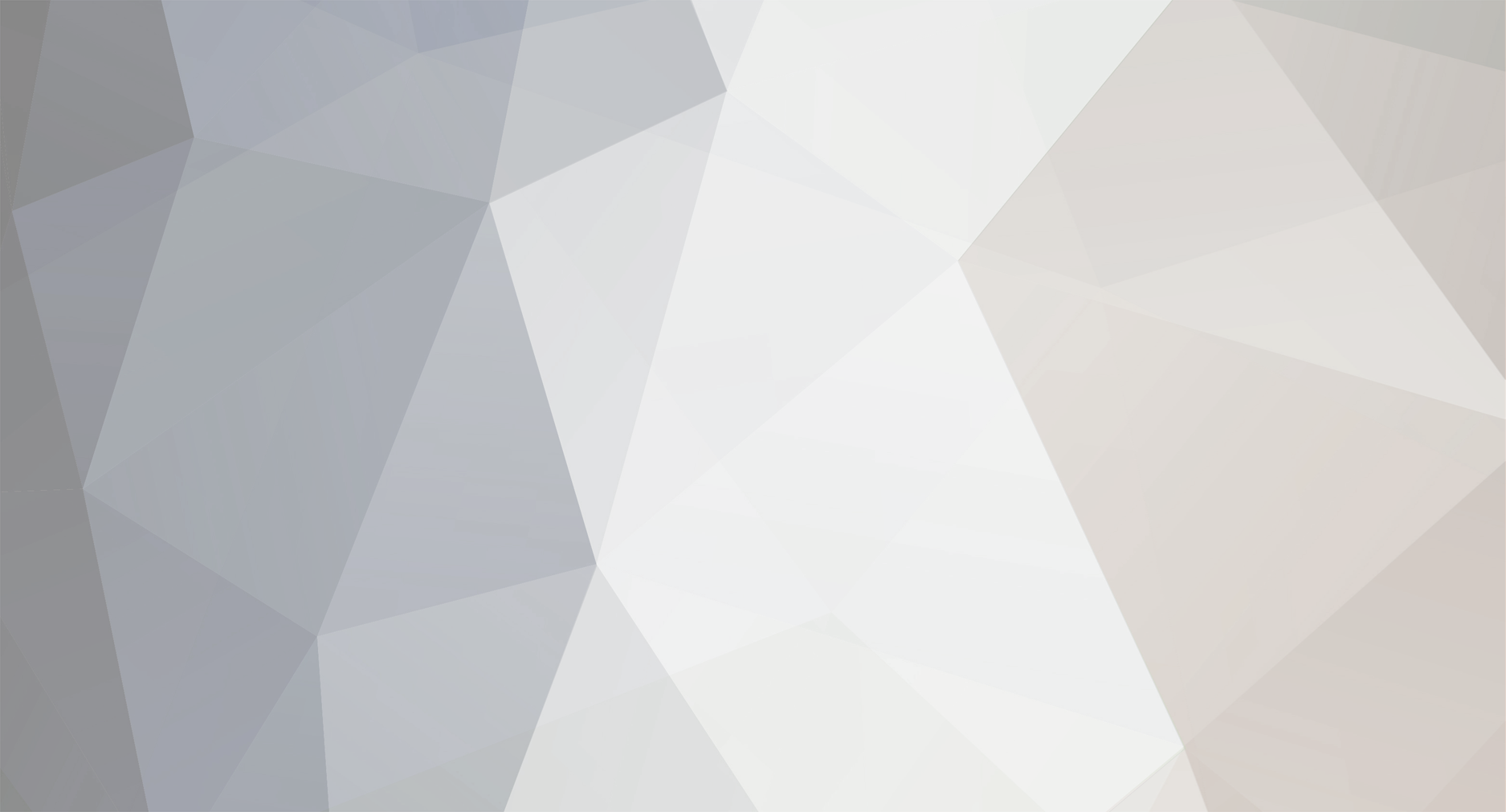
bruhaw
-
Posts
179 -
Joined
-
Last visited
-
Days Won
1
Content Type
Profiles
Events
Forums
Gallery
Downloads
Community Map
Posts posted by bruhaw
-
-
What were your compression readings? As long as around 140-150 and not huge variances you would be good.
-
From what I understand there is no difference between a t2 and t4 even though the t4 is heavier. They didn't beef them up any and just used the same shock. Not sure about on the new models but all the older ones had the same. There is a difference in mounting points and shock height on the earlier T4's and T2's with the front gas tank with the early ones having a longer shock up front along with different mounting points. They only had those on some of the early models and then they changed on the 2009 models to what most everyone probably has on their Joyner. If the gas tank is up front the shock is longer though.
-
Rocmoc or Lenny - what air pressure do you run at with the 31" tires. I am running 30" BFG's and figured you two have played around with it enough to know the best pressure to run at with them.
-
What tapered bearings did you use? Ones from Casey at JMC - S31 is the part number I believe. I just put the bearings in my hubs this past week but have not installed as I was rebuilding both front and rear diffs. Going to put it all together this week sometime but wondering if I will run into same problem as you two with the new bearings.
-
Just awesome looking and totally functional. That is one nice cargo bay. Nice work as usual Lenny.
-
-
Do you have the owners manual as it will show all the fuse locations? If not I can send you the manual in PDF form. It will help for other things that come up as well. But yes the fuel pump fuse is behind the driver seat. You also have a fuse box under the dash on the passenger side. The manual gives all the fuses and locations so it helps narrow it down quickly.
-
Welcome to the Joyner Forum! Those who join can never leave though. Couple of things. One - are you waiting for the gauges/rpm to cycle through and go back to 0? If you try to just start without doing this it will just crank. After it has run for a while and it just dies then you could just hit the key and it should start but first time starting after sitting you have to let it cycle through. Second when you turn the key in just the on position and if the gauges do cycle through and then come back to 0, can you hear the fuel pump running at that time. If you don't then it could just be a fuse. This fuse is located right by the ECM behind the driver seat. If you have the manual it will show in there which fuses are which. There are many posts on this topic if you use the search option on the top right hand corner of this page. You will find a lot of Q&A on this. Sometimes it is something simple, other times much more difficult.
-
They are threaded inside the tubing and all I did was remove and install the new ones. No welding on my end.
-
http://www.vxb.com/page/bearings/CTGY/HR
I replaced all of my heims joints including the tie rod ones which are smaller and use a needle style zert fitting. All of the other heims joints have the regular standard zert fitting. Mine were squeaking all the time and once I replaced them all - no more squeaking and I can grease after every outing if need be. I tried the rubber boot covers but they kept binding up and tearing so I don't and can't use them. Lenny was able to get them to work on his and I got the idea from him at the jamboree but no luck on mine. Either way they do get dirtier now but I can wipe off and just grease again. See link above. The ones we use are all right hand thread and16mm for all the larger ones and 12mm for the tie rods. POS16 and POS12 are the part numbers. Not too expensive either and well worth getting rid of that damn squeaking!
-
1
-
-
Easiest way I found after reviewing all the posts was to rent a slide hammer and FWD Axle Puller adapter from Autozone. Slide hammer is part # 27033 and Axle Puller is 27058. Took me about 1 minute or so to pull each CV off the diff. Some went in 10 pulls and others took about 20 but all were rather easy. I pulled both front and rear diffs as I am changing gearing to Renegade and doing Lenny's rebuild kits. Pictures of puller is on my gallery.
-
I second Dedub on getting them from Casey. Just got 4 a few weeks ago as he was on backorder for a while and finally got some in and shipped them out to me. Hopefully he has some in stock. When I rebuild my diffs I am going to replace all 4 to be on the safe side.
-
Thanks Kinarfi for the instructions on doing this and the detailed PDF from Casey!! Hope not to need them ever but you never know with these Joyners.
-
DirtyDog, how many rolls does it take? 1 or 2 to do all 4 fenders?
-
I run King Shocks on mine and have not noticed that at all. Ride does not get hard and I mainly do trailing riding.
-
State farm full coverage fro $250 or so. 2 Quads, 20ft enclosed trailer, Joyner t4 for $600 a year, so they are not bad either.
-
How long of bolt did you go with? I used the 55 and had no issues.
-
12MM worked fine on mine and I had to drill out with ball joint in so that bolt would go through so I know that it definitely was interfacing with the ball joint. There is not much of a difference and with the 12MM you would use a 15/32" drill bit and you will be set. Use cutting fluid when drilling it out as it will be easier on the drill bit and you will get it done faster.
-
Kinarfi - I put a pretty clear picture of the A-arms / ball joints in the picture gallery. If you look at that you can probably tell if it is a different configuration or not. I was able to get both the upper and lower ball joints in the picture along with the surrounding area. Might be different but that is hard to imagine it would be.
-
Turned both ways and it is not close to hitting anything. So, looks good. From the way it looks it would have to be a pretty long bolt through the ball joint to come close to hitting the A arm.
-
Kinarfi - I have very little bolt thread past the nut - only a few threads. The other night when I did one side I did check when completed and it wasn't hitting anything. Had the wheel off and was able to go back and forth without interference. Will check again the other side too but think there is no clearance problem at all.
-
Went with 12M X 55 X 1.75 and the shoulder was exactly the same as the stock 10M. Easiest way to do was to pull the wheel and jack up under lower control arm to put pressure on both upper and lower joints. Drilled out with a 15/32 and this included the ball joint area as I left them in like Lenny and Kinarfi said to do but not after doing only one with the joint out and then not being able to get the bolt to go through without hammering it in. So learned my lesson on the other 3 and left the joint in and just drilled away. Went back and did the other one the right way. Did not tap but rather put a washer on the nut side and used a Nylock nut which by the way is grade 8 along with loctite. So there are Nylocks that are grade 8. Was able to torque to 100 pounds and the clamp that locks the ball joint in has no gap in it unlike before where there was a decent amount there. Besides being clamped tight the shoulder on the 12M will hold it in there very well. Wish I would have done all of this when I changed out all the ball joints with zert fittings and new urethane bushings but OH well. Thanks for bringing this up Tinman. I know this goes way back to 2009 when Lenny and Kinarfi and others had problems. I figure better safe than sorry as it would cost a helluva lot more if it popped out at a higher speed in bad terrain. Done now and on to the next project whatever that may be. Thanks Guys!
-
Thanks guys for the replies. I was going to use a Nylock nut with the loctite as well. Ok to use the Nylock? I don't think it is grade 8 though. Not sure if they even make a grade 8 Nylock.
-
Lenny - what if you just drilled it out for a 12 mm using a hardened bolt and lock nut and did not tap it out. It would then be more like a clamp and with the hardened bolt you could torque it very tight. The shoulder on the bolts I am using match up with the stock ones so there is no problem there with mating to the ball joint notch. What do you think? Any opinions?
HELP-Trooper T4 won't start
in Joyner UTV SxS Forum
Posted
Are you cranking it until you get the highest reading. Should be 5 cranks or more. If so, then the compression is real low and the variance between two of your cylinders is 20% and that is not good either. T